Do you manufacture or import candles? Know your responsibilities
Legal Requirements for Candle Manufacturers and Importers in the EU
Manufacturers and importers of candles — including scented waxes — operating within the European Union are subject to specific legal obligations designed to protect both human health and the environment. These regulations serve not only to ensure consumer safety, but also to promote responsible manufacturing and transparent practices across the supply chain. Compliance strengthens brand credibility and helps minimize the risks associated with trading chemical-based products in the demanding EU market.
Candles as Chemical Mixtures Under REACH & CLP
According to REACH (Regulation 1907/2006) and CLP (Regulation 1272/2008), candles are considered chemical mixtures. Therefore, they must meet detailed requirements regarding their classification and labelling.
If a candle is classified as hazardous:
- The supplier assumes additional responsibilities before placing it on the market.
- The product must be correctly labelled and packaged in line with CLP regulations.
The responsibility for classification lies primarily with the manufacturer or importer, while compliant labelling must be ensured by every supplier within the distribution chain.
Ingredient Classification & Safety Data Sheets (SDS)
A candle’s classification depends on the specific ingredients and their concentrations. Information about each component’s classification should be obtained from:
- Raw material suppliers (for manufacturers producing their own candles), or
- The supplier of the finished product (in the case of importers or distributors).
This information must be clearly listed in Section 3 of the candle’s Safety Data Sheet (SDS) provided by the supplier.
Safety Data Sheet
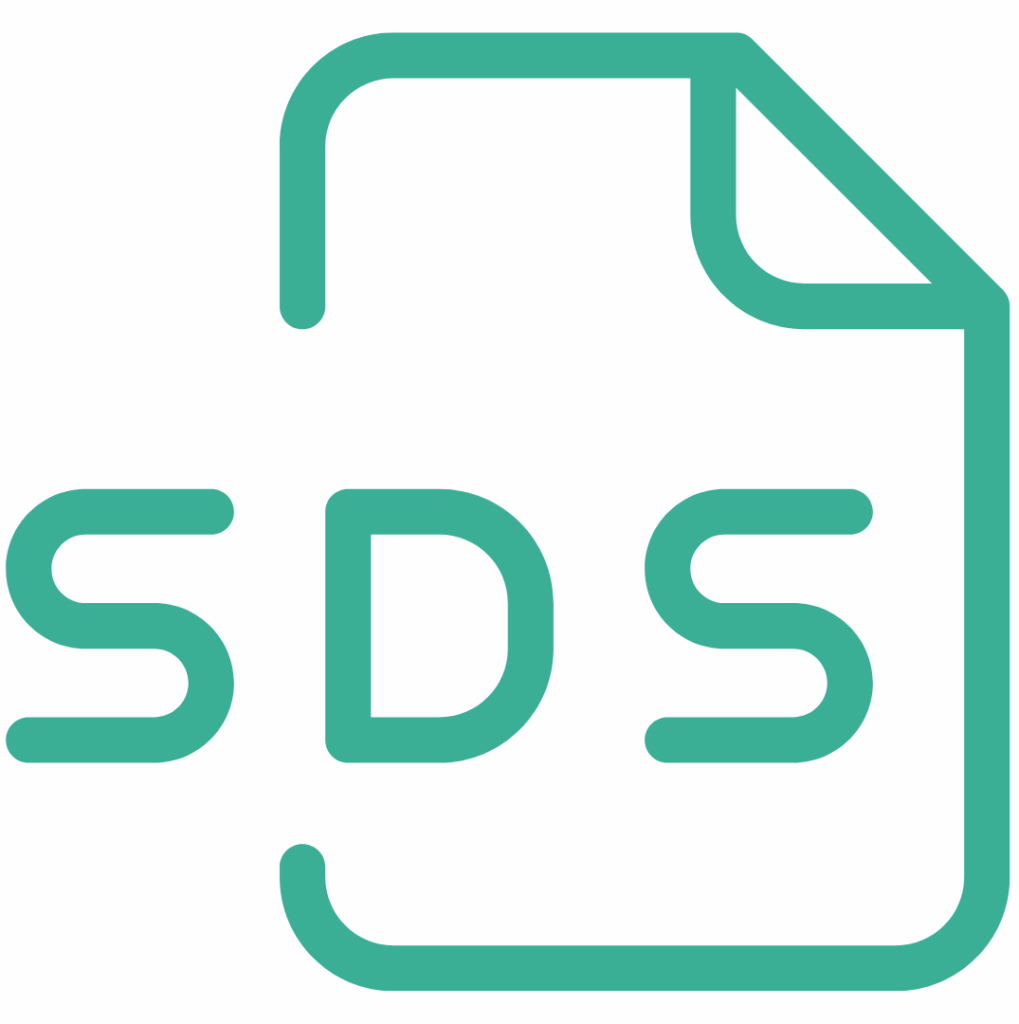
A Safety Data Sheet (SDS) is essential for candles classified as hazardous. The SDS contains detailed information about hazards and safe usage of the product and must be prepared in accordance with Commission Regulation (EU) 2020/878 in the official language(s) of the country where the mixture is marketed. If candles are sold directly to consumers, an SDS is not required; however, the candle label must include all required information as per CLP regulations.
If you do not supply products directly to end-users, for example: if you provide candles for resale, you must supply the SDS to the distributor or retailer. An SDS is also required if the product is intended for professional use, such as in restaurants.
In some cases, an SDS for an unclassified candle must be made available upon request from the recipient. This applies when the mixture contains:
- at least 1% by weight of a substance hazardous to human health or the environment;
- at least 0.1% by weight of a substance classified as carcinogenic (Category 2), reproductive toxicity (Categories 1A, 1B, or 2), skin sensitizing (Category 1), respiratory sensitizing (Category 1), affecting lactation, harmful to breastfeeding children, is Persistent, Bioaccumulative, and Toxic (PBT) or very Persistent and very Bioaccumulative (vPvB);
- or a substance with a Community-established occupational exposure limit (OEL).
Safety label
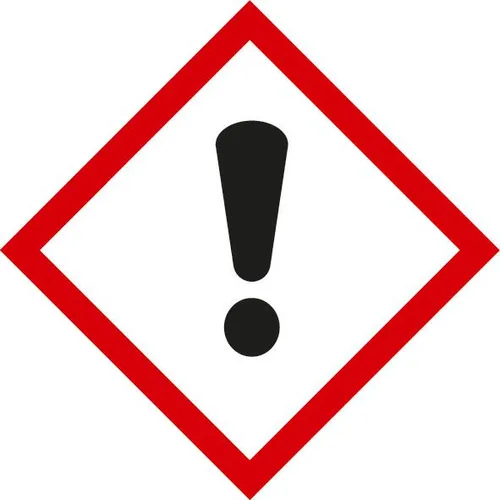
A hazardous mixture must be packaged and labeled according to CLP regulations. A CLP label cannot be applied directly to the wax of the candle, as it is considered a mixture, not packaging. Furthermore, an open glass container, an aluminum tealight base or an openwork paper box is not deemed suitable packaging for hazardous mixtures under CLP. A candle in such a container must be provided in packaging that meets CLP requirements. The label must be permanently affixed to the surface of the packaging that directly contains the candle and positioned on the side to allow easy horizontal reading of the text.
A CLP-compliant safety label must include several essential elements:
- the name, address and phone number of the supplier(s);
- the nominal quantity of the product;
- hazard pictograms;
- signal words;
- hazard and precautionary statements;
- product identifiers (for mixtures, this includes the trade name or the designation of the mixture and the identity of all substances in the mixture that contribute to the classification of the mixture as regards acute toxicity, skin corrosion or serious eye damage, germ cell mutagenicity, carcinogenicity, reproductive toxicity, respiratory or skin sensitisation, specific target organ toxicity (STOT) or aspiration hazard);
- supplemental information (EUH statements, if applicable).
The CLP regulation also specifies, among other things, the minimum size of the label and pictograms, the arrangement of label elements, and rules for using fold-out labels. The forthcoming version of CLP, which has yet to be officially published, will also regulate the minimum font size.
Notification to the Classification and Labelling Inventory
If you are importing a candle, a perfume blend or any other mixture or a substance for candle production, you may be required to submit a notification to the Classification and Labelling Inventory. Hazardous substances, whether imported as pure substances or in mixtures, must be reported to this registry regardless of the tonnage.
Poison Center Notification (PCN) and Unique Formula Identifier (UFI)
If a candle is classified as hazardous to human health or due to its physical properties, it must be reported to Poison Centers (known as Poison Center Notification – PCN) in the countries where it will be marketed. A key part of the PCN submission is the UFI code, which must also appear on the product label. The UFI (Unique Formula Identifier) is a unique 16-character alphanumeric code assigned to a specific formulation, allowing Poison Centers to quickly access product composition information, which is crucial in emergencies.

REACH Registration
Any substance manufactured or imported in quantities exceeding 1 ton per year is subject to registration under REACH. This applies to both pure substances and substances within mixtures. For imports, the quantities of imported substances (primarily paraffin in the case of candles) should be closely monitored, and REACH registration must be completed upon exceeding 1 ton per year. When sourcing raw materials from EU suppliers, compliance with REACH should be ensured by the respective contractors.
SCIP Database Notification
Candles are considered a combination of a mixture and an article. If an article contains substances of very high concern (SVHC) in concentrations above 0.1%, it must be reported to the SCIP database. For instance, boric acid in the candle wick may require such notification. The SCIP database was established under the EU Waste Framework Directive to identify products with potential environmental and health impacts. It includes a product category covering “Candles and similar articles.”
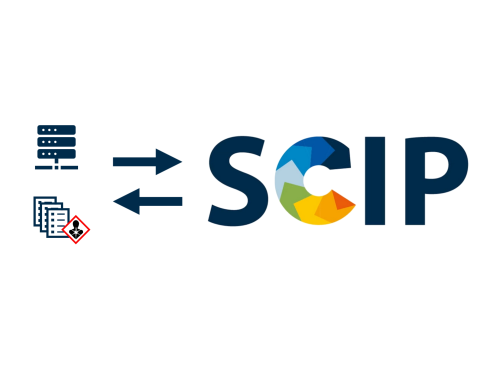
Safety Standards for Candles
In addition to compliance with REACH and CLP regulations, candles must meet certain quality standards, including:
- EN 15426 (Specification For Sooting Behaviour),
- EN 15493 (Specification for fire safety) and
- EN 15494 (Product safety labels).
Adhering to these standards is essential for product safety and market compliance. Extra labeling requirements, separate from CLP labeling, may also apply.
Compliance with EUDR
Regulation (EU) 2023/1115 on deforestation-free products (EUDR), we have previously discussed on our website, may also apply to candles. If materials like palm oil, palmitic acid, stearic acid or glycerin are used in candle production, European manufacturers will likely be subject to this regulation. Key obligations include:
- collecting and verifying data on the origin of raw materials produced after 2020, ensuring that the raw materials used do not contribute to deforestation;
- ensuring transparency in supply chains;
- documenting compliance with EUDR requirements.
Companies must implement due diligence processes to demonstrate that their products are not linked to deforestation.
Challenges and support in meeting legal requirements
Legal requirements for candle production and import can seem complex, but compliance is essential for protecting user health and the environment. For professional assistance, please feel free to contact us.